Globally connected, regionally rooted
Our precision products “Made in Germany” are manufactured in Aachen and distributed in more than 20 countries. Our production area of more than 39,500 square meters and the high-performance machinery in operation there enables us to offer an arguably unique in-house production depth compared to competitors in this sector. That is why even highly-complex components requiring far more than 30 process steps never need to leave SCHUMAG production plant. We call it “Vertical Quality Assurance”. For our customers this guarantees fast, flexible AND highest quality production.
From concept to production:
We are specialized in the production of high-precision components following the requirements of our customers. From the first sketch to the delivery of the finished component we offer all the manufacturing steps – no matter whether for a unique piece or on an industrial level for up to 60 million per year.
Based on the customer’s component drawing, SCHUMAG develops the complete process chain from the raw material to the finished part. Process chain development, process step specifications, drawings and production instructions are designed and calculated for the required quantity scenarios. Design and process requirements are scrutinized and coordinated with a focus to optimizing economic efficiency.
With initial sample and prototype production on series machines, SCHUMAG offers a unique advantage for a risk-free transition to series production.
The end result is a process chain that optimizes series component costs and delivers specification-compliant components in a reliable, stable process.
- Drawing analysis, design of the process chain, calculation
- Process step analysis of industrialization and production costs
- Risk analyses, FMEA, alternative process step considerations
- Scrutinizing of functional and process-related tolerance requirements as well as effort and cost calculations of the manufacturing processes with the customer
- Support with material design
- Supporting the development process from the first prototypes to the SOP
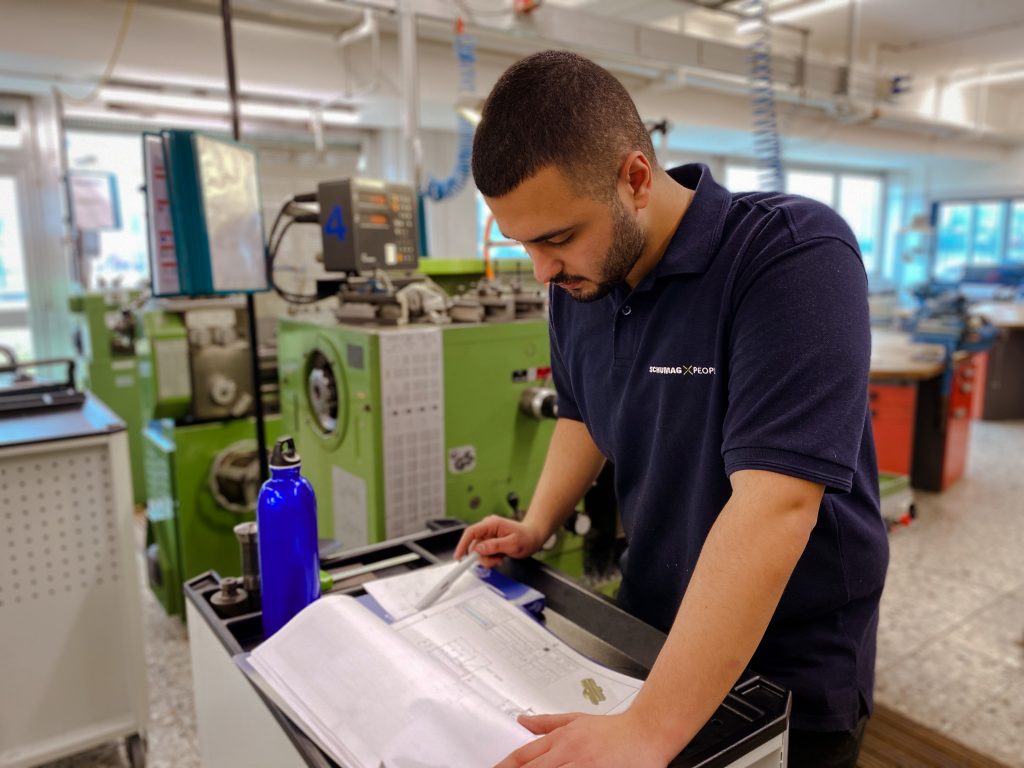
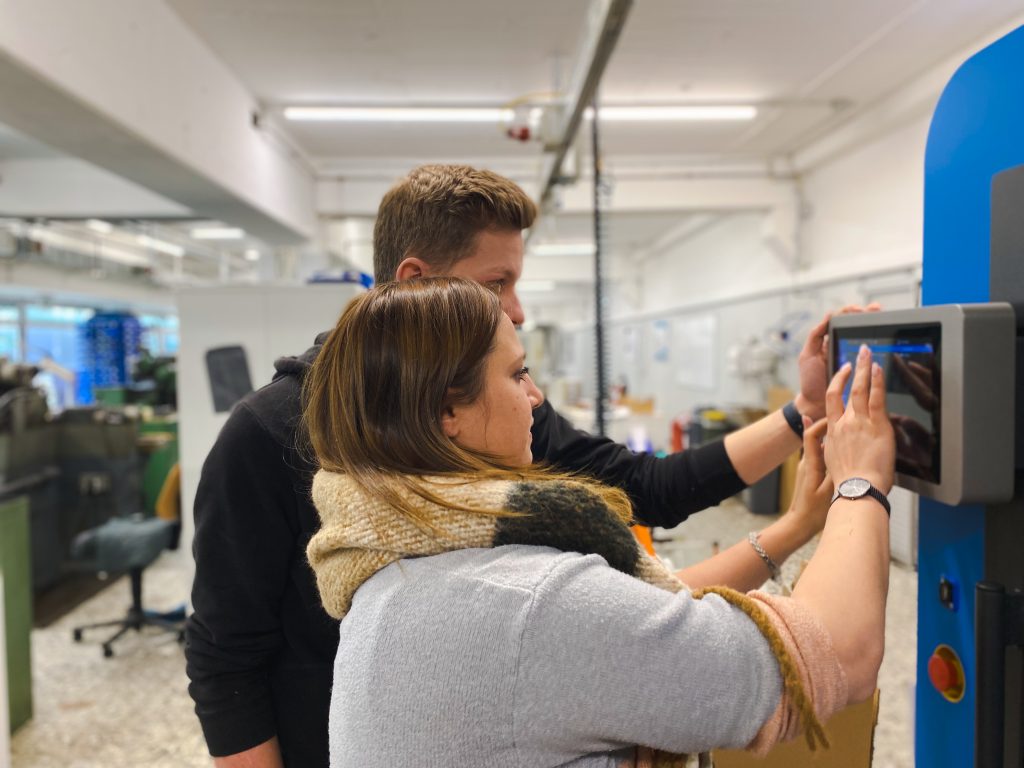
With the processing of bar stock exclusively from renowned manufacturers in selected grades, most of the strictly traceable processing steps begin in SCHUMAG`s precision components production. Apart to testing the material composition we often start processing with grinding the bar diameter section.
- procurement of materials according to customer requirements
- large stock of various special alloys
- support with material design upon request
- independent in-house goods inspection (spectral analysis, hardness testing, texture examinations)
- in-house raw material preparation (bar grinding, chamfering of bar materials)
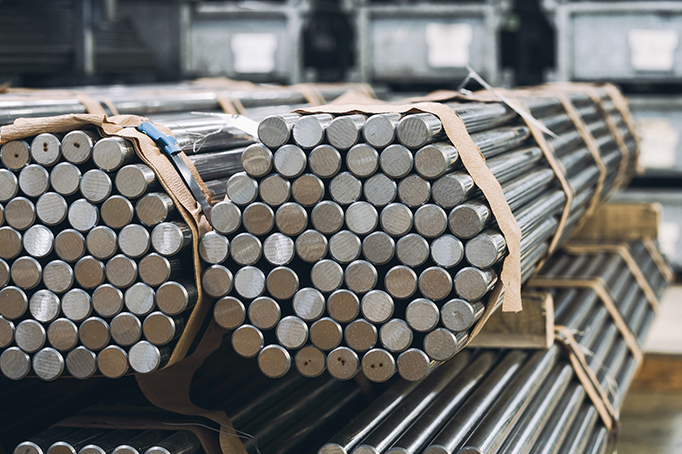
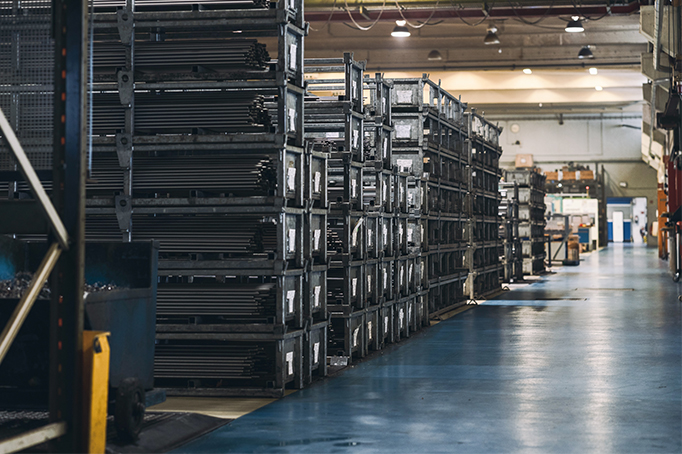
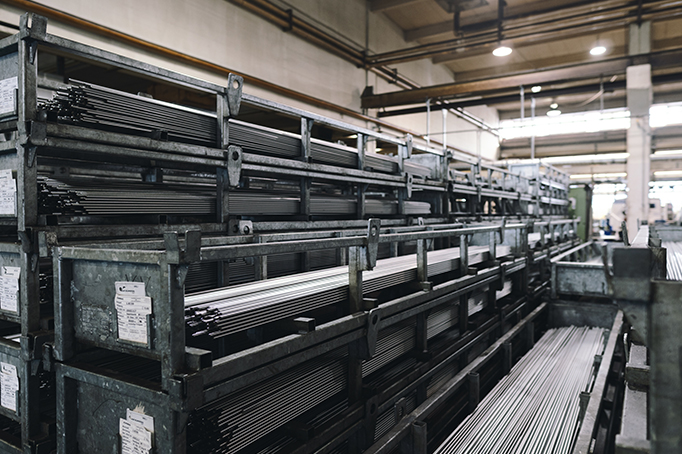
Proper soft machining forms the basis for the cost-efficient and stable production processes of most precision components. SCHUMAG uses an extensive and diverse range of machinery for this purpose, but also involves external partners for specialized tasks when needed.
- short bed lathes with up to three revolvers and up to 36 driven tools, bar aperture up to 65mm
- multi-spindle lathes with up to 8 spindles (conventional and CNC)
- long bed lathes with up to 8 axles (diameter from 2-32mm)
- deep-hole drilling (diameter 1-15mm)
- milling 3- /4- /5- axle-machining with up to 48 tools
- ring lathing automat 0.3 – 6mm
- thread / roll knurling
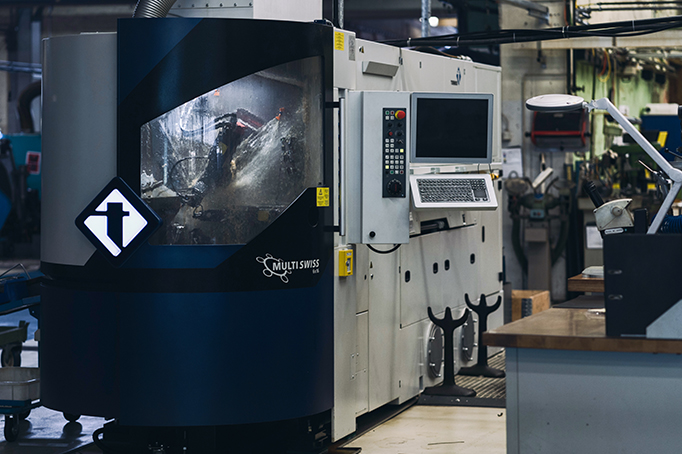
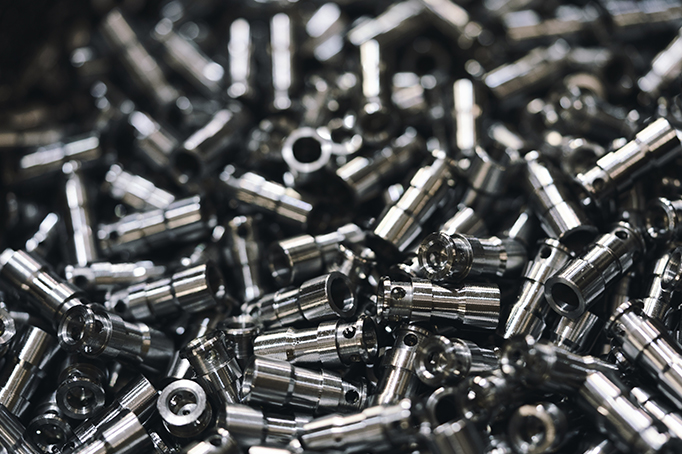
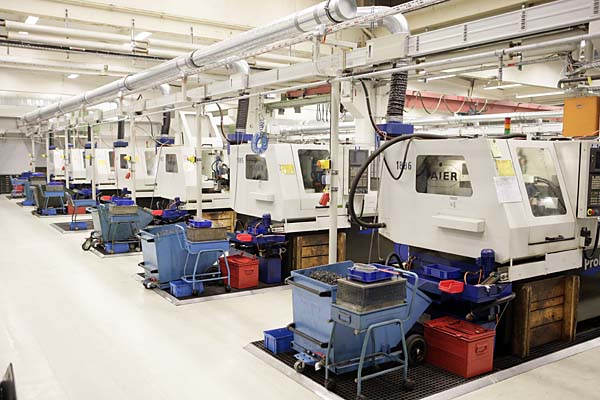
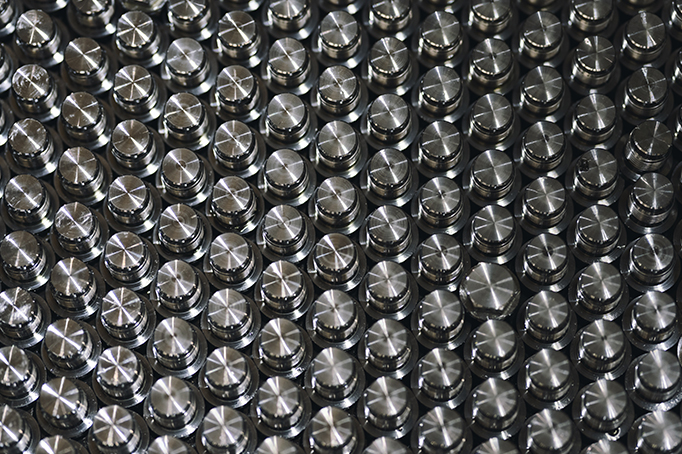
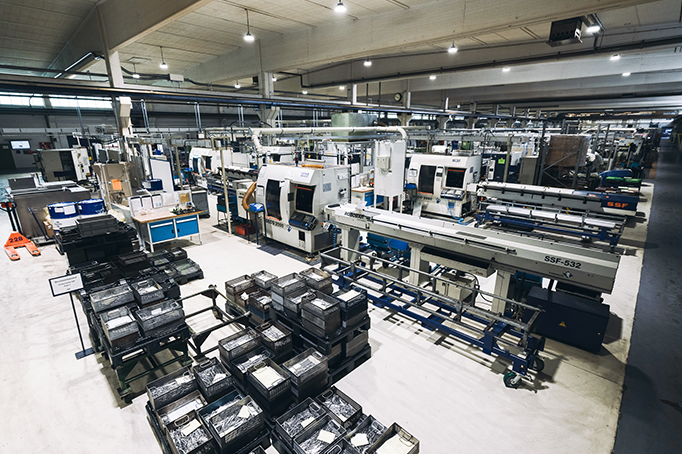
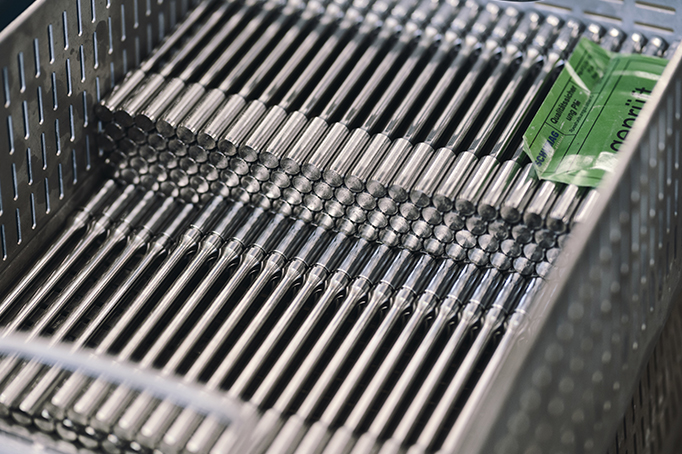
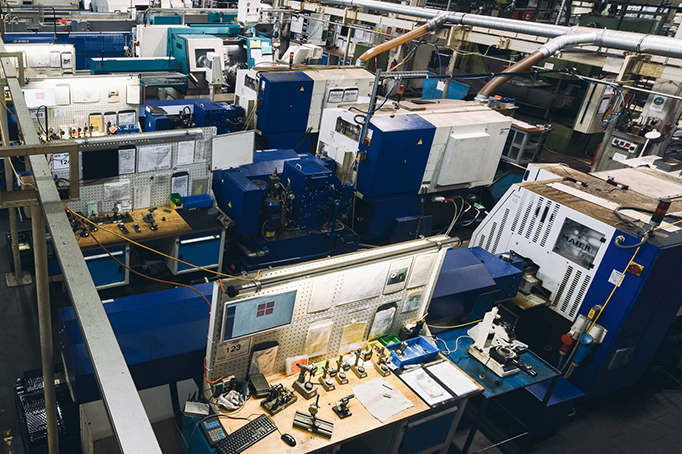
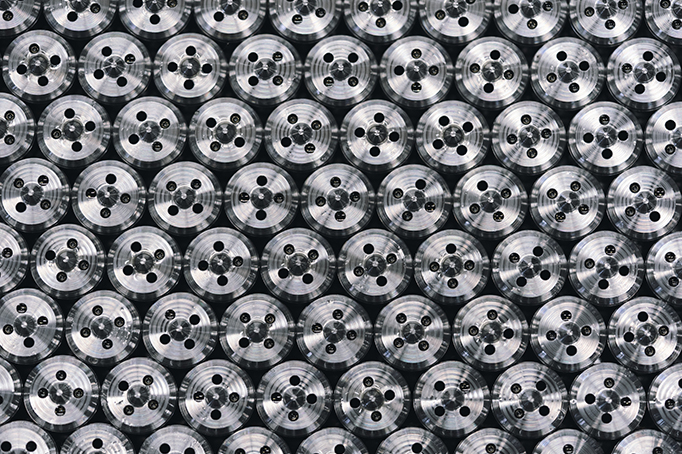
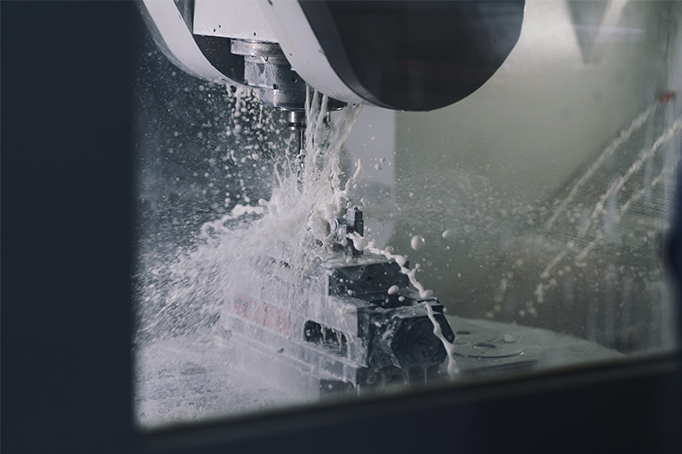
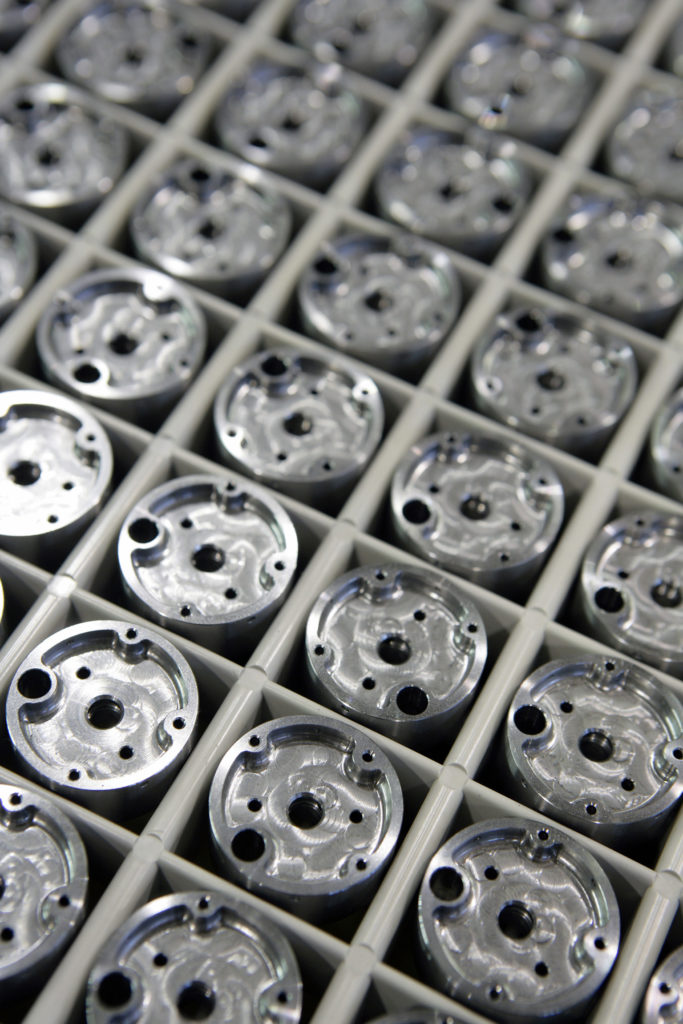
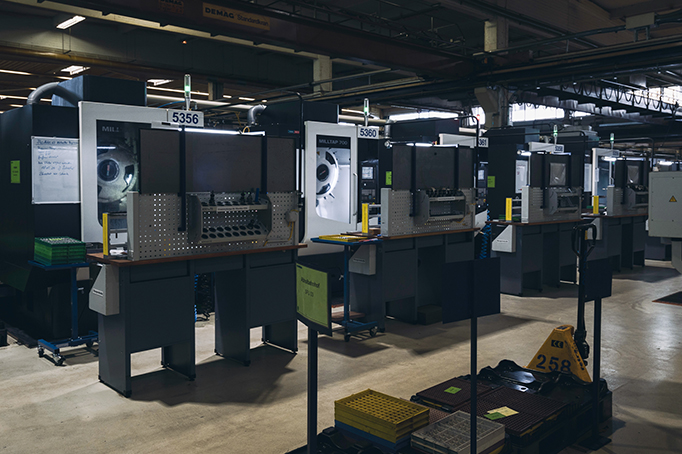
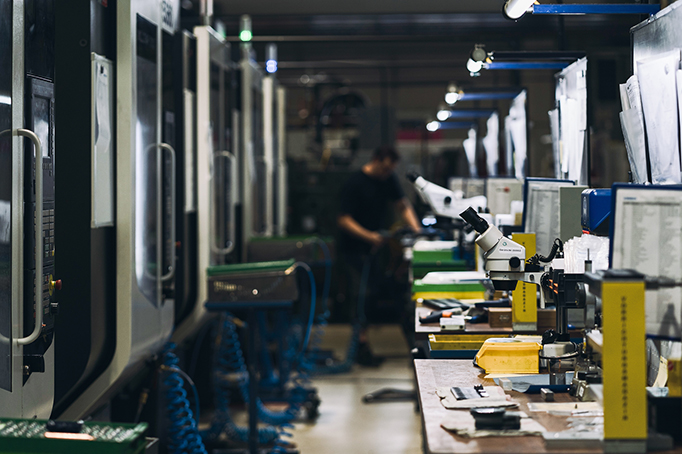
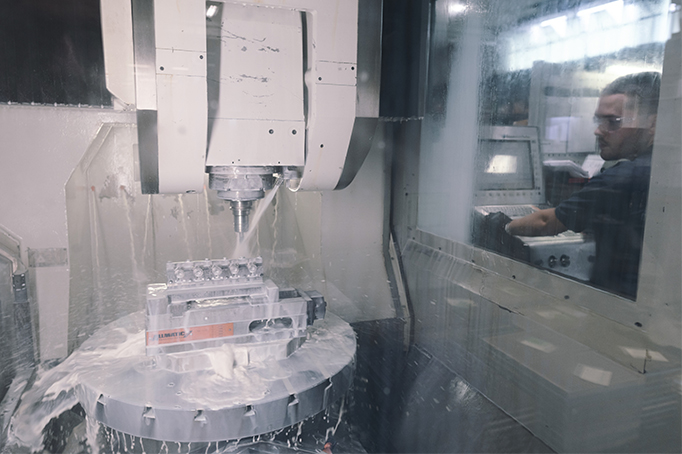
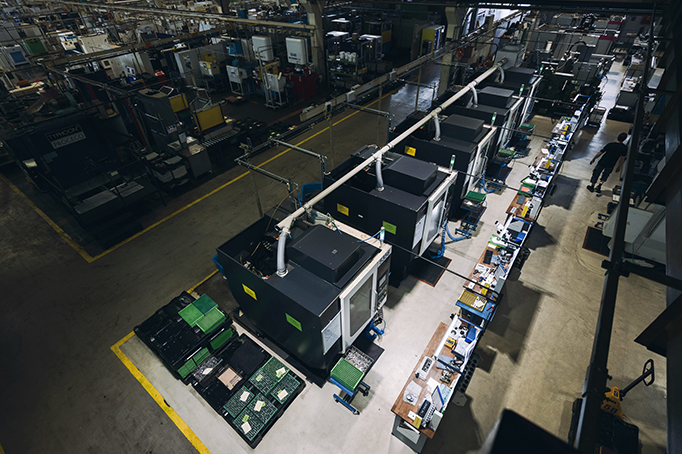
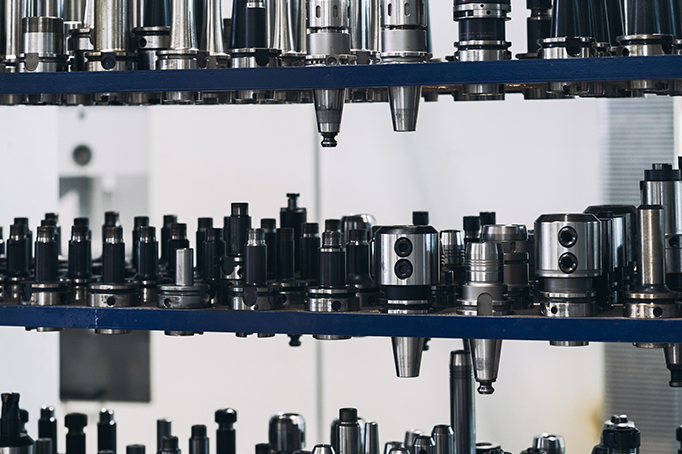
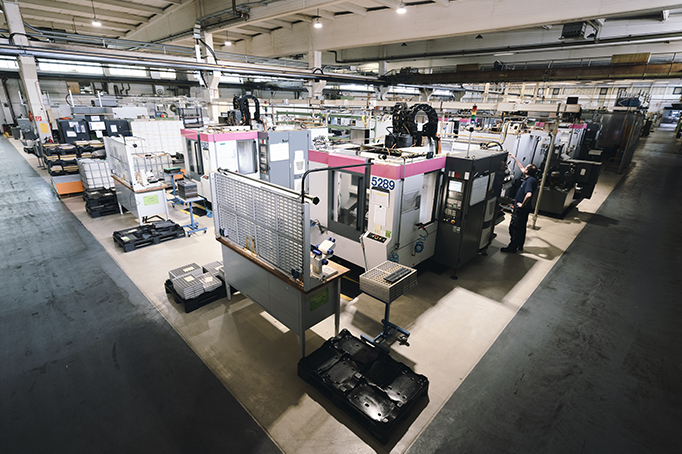
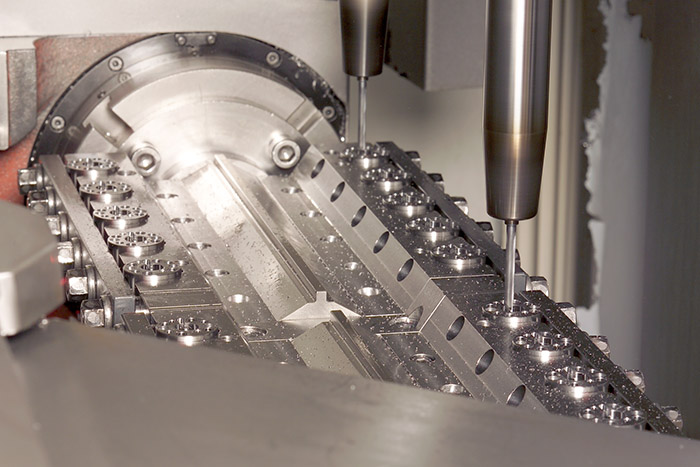
Special components of injection systems require extremely smooth surfaces as well as rounded edges and burr-free finishes. In order to carry out suitable deburring even for complex geometries SCHUMAG offers a unique variety of deburring techniques either in-house or through external partners.
- thermal deburring
- abrasive flow grinding (DFL)
- centerless / plunge brushing
- glass bead blasting
- Vibratory finishing
- ECM-deburring
- sinker EDM
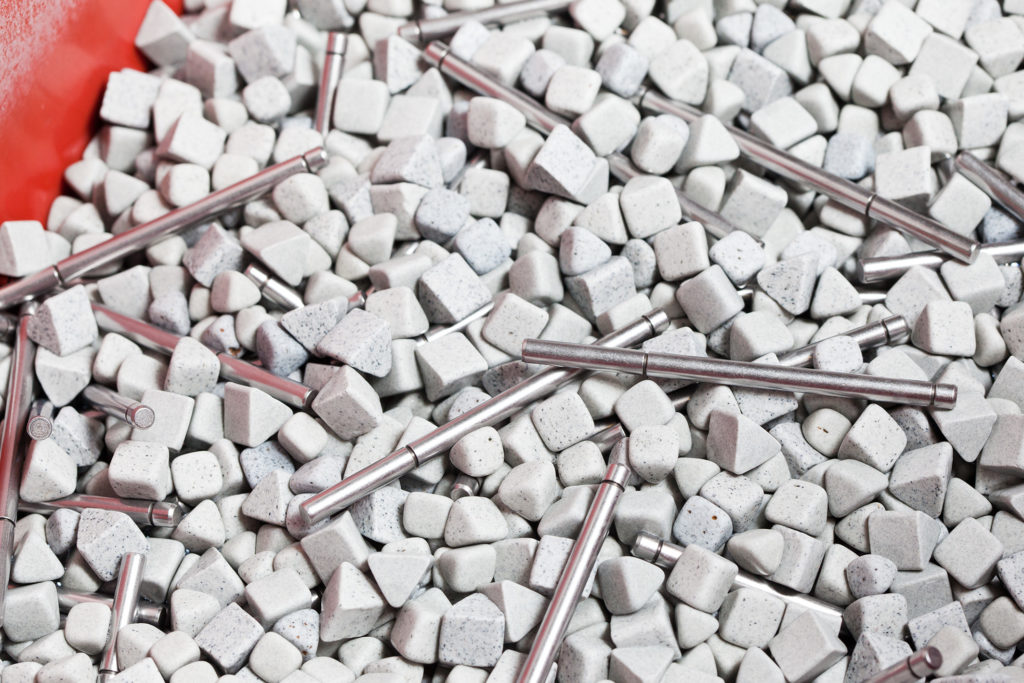
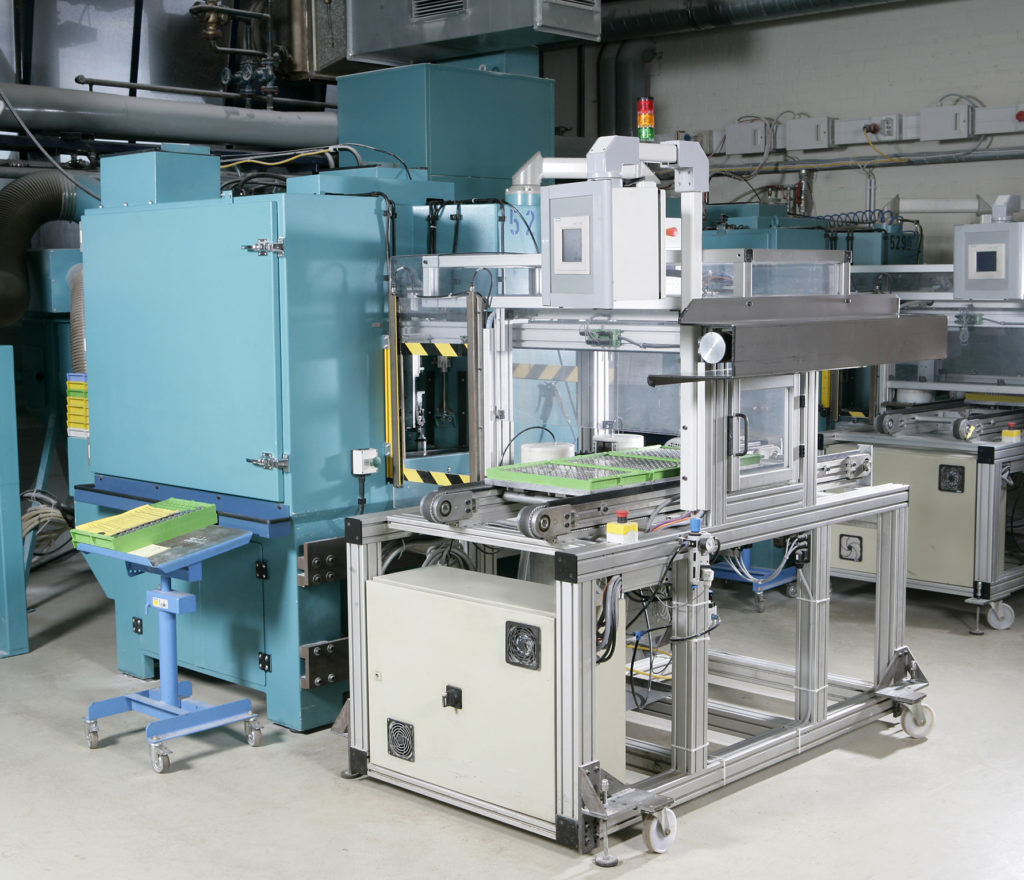
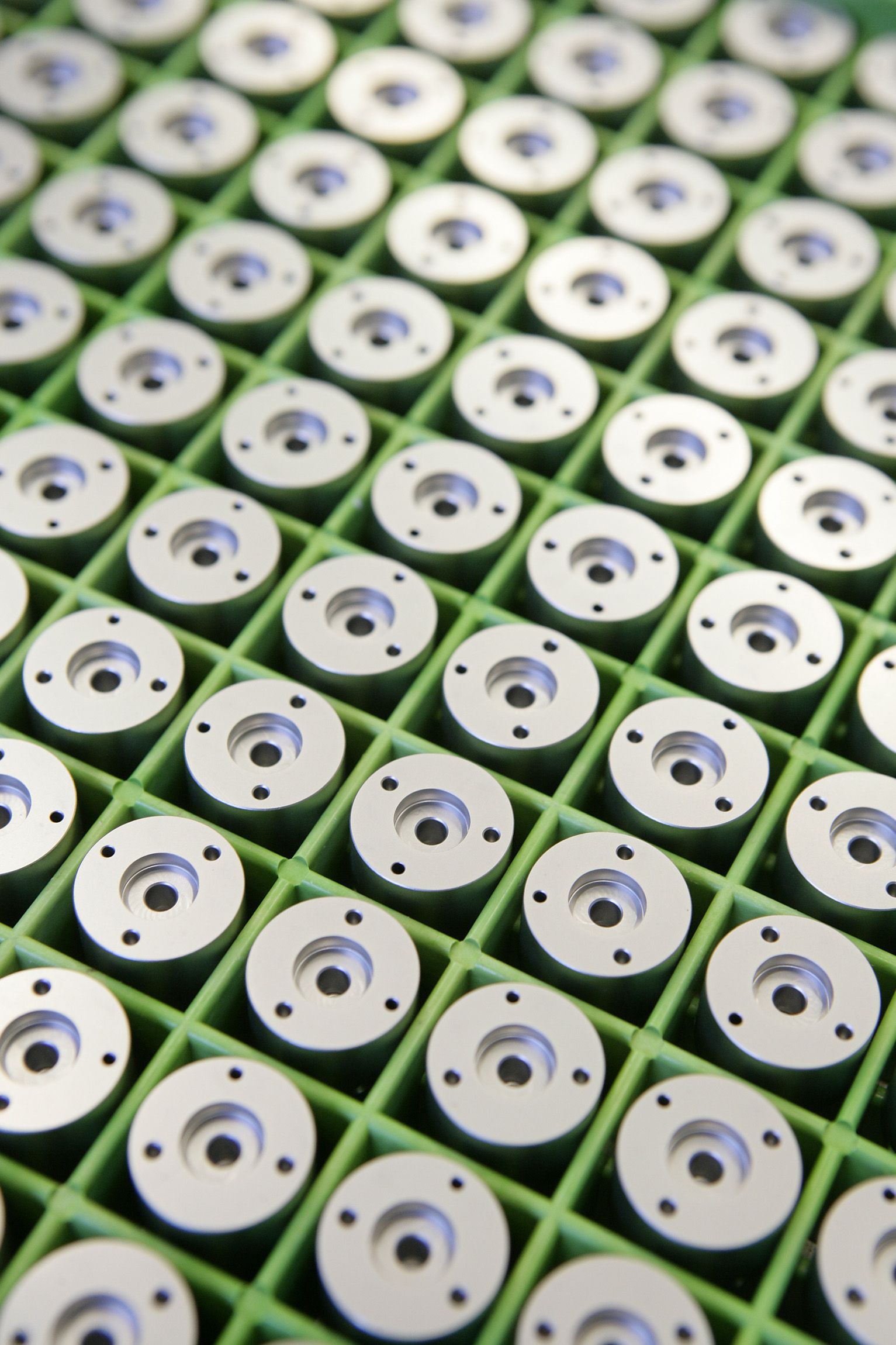
For hardening processes, it is essential to apply the correct and reliable method suited to the material and the hardening target. SCHUMAG offers extensive in-house expertise for these methods, which is key for streamlined production of medium batch sizes in long process chains.
- protective gas hardening
- case hardening
- salt bath hardening
- vacuum hardening
- case hardening vacuum (LPC)
- gas nitriding
- gas-nitro carbonizing
- tenifer treatment
- salt bath nitriding (QPQ)
- annealing
- HF hardening (partial inductive hardening or soft-annealing)
- HF bar hardening (bars up to 3m)
- super-cooling (chamber: minus 80C°; or nitrogen: minus 196C°)
- well-equipped hardening laboratory for all established material analyses (hardening tests, sample preparation, microstructure analyses)
- special component cleaning of entire furnace charges (purification plant)
- belt blasting system
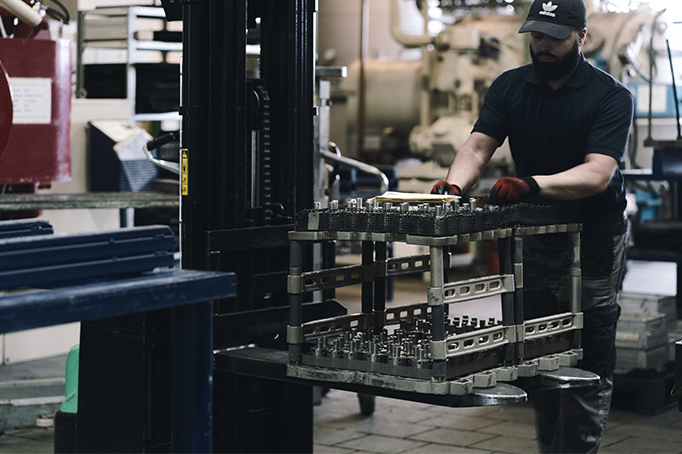
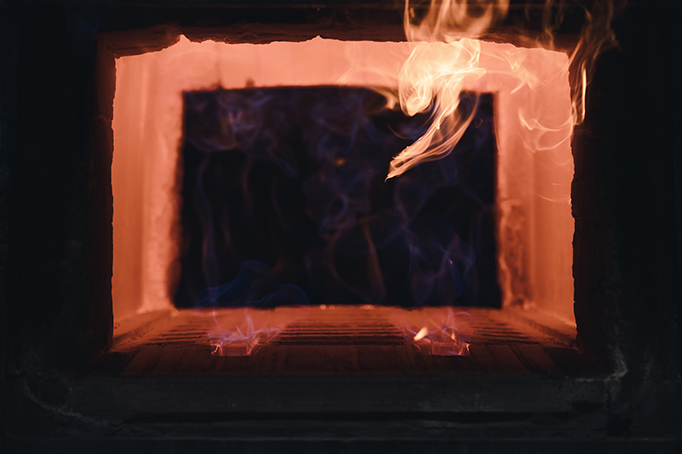
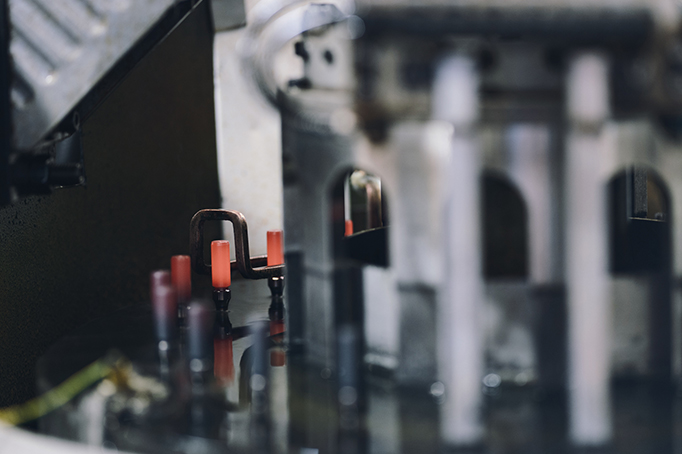
For almost 200 years, SCHUMAG has been all about precision. The precise hard machining of serial components is now practically embedded in SCHUMAG’s DNA. Therefore, it is not surprising that today we can offer a unique range of grinding methods and the corresponding experienced specialists. Only this combination ensures that stable, efficient processes can be developed and in a short period of time.
- grinding
- external cylindrical grinding centerless
- external cylindrical grinding with plunge-cut centerless
- external cylindrical grinding between centers (straight/angled)
- internal grinding
- surface grinding
- lapping
- honing
- internal cylindrical honing
- flat honing
- double-sided surface grinding
- superfinishing
- flat superfinishing
- external cylindrical through-feed processing
- external cylindrical plunge processing
- vibratory finishing
- vibratory bowl machines
- centrifugal disk finishing machines
- high-gloss polishing
- rotary barrels
- hard turning
- hard milling
- micro grinding (own micro grinding machines)
- abrasive flow machining (flow calibration and DFL)
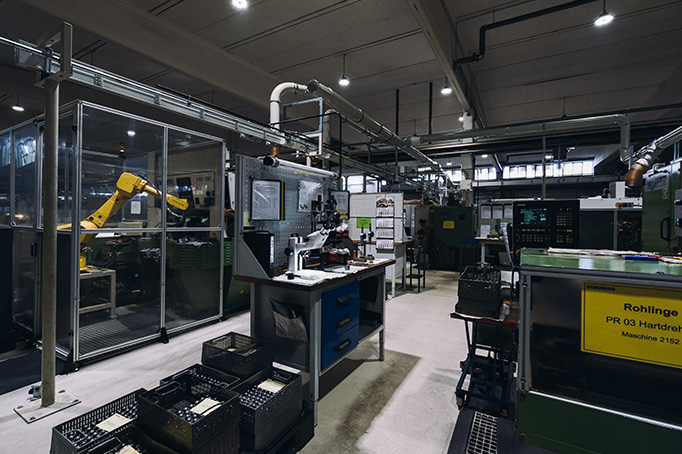
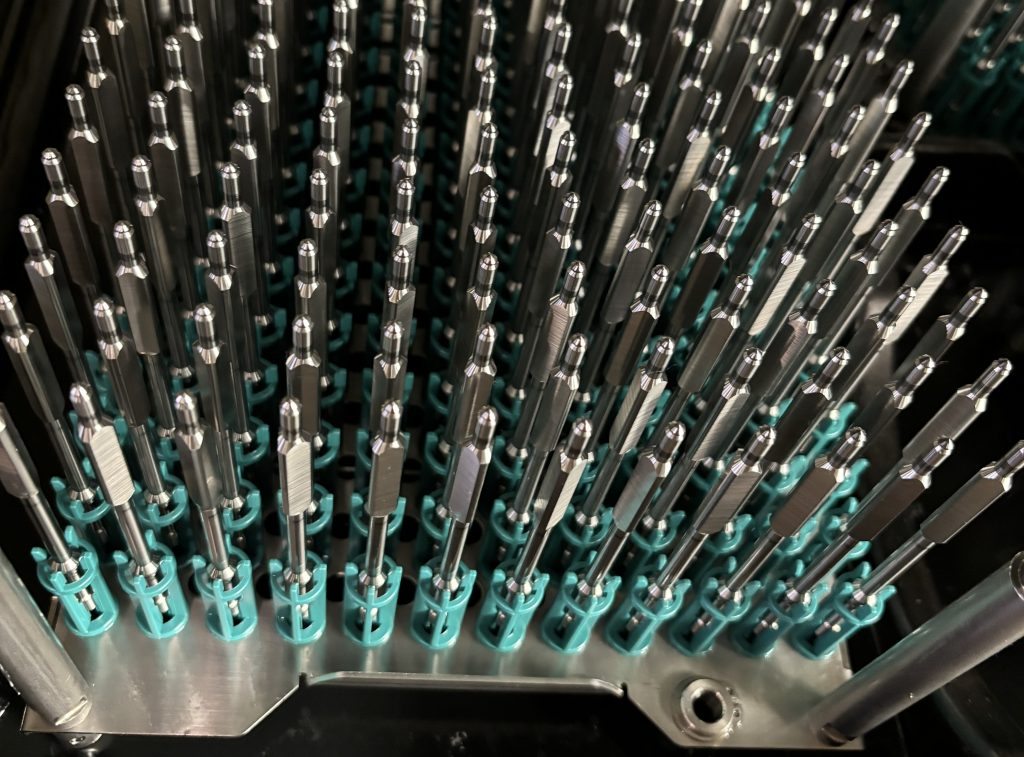
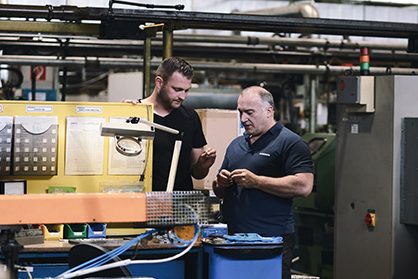
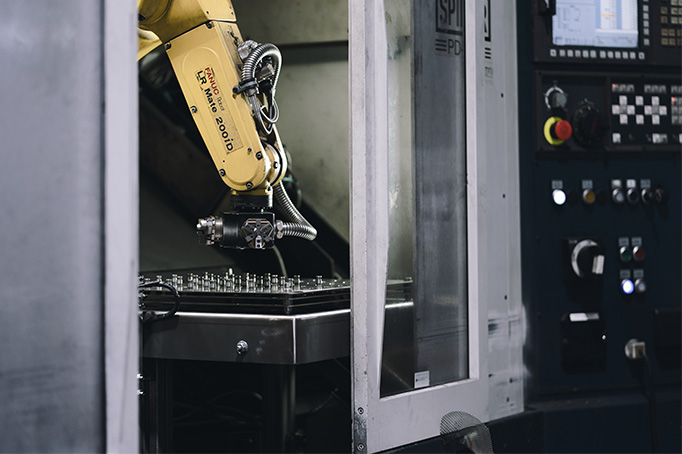
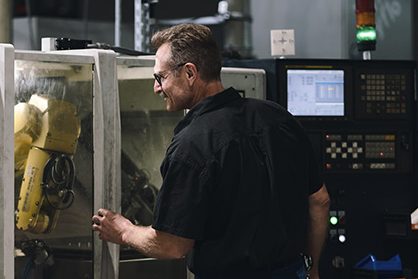
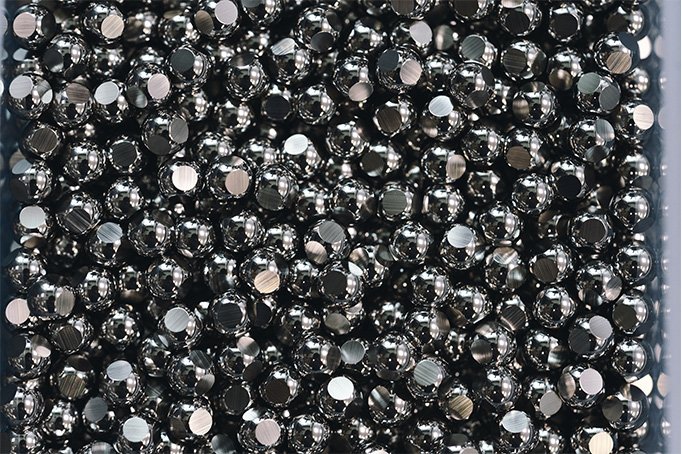
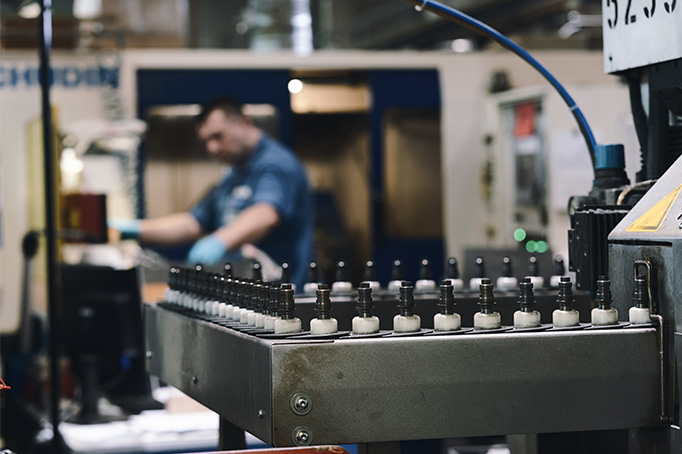
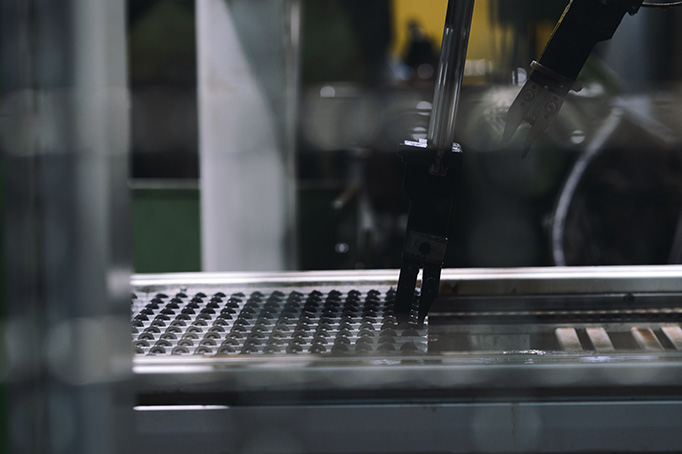

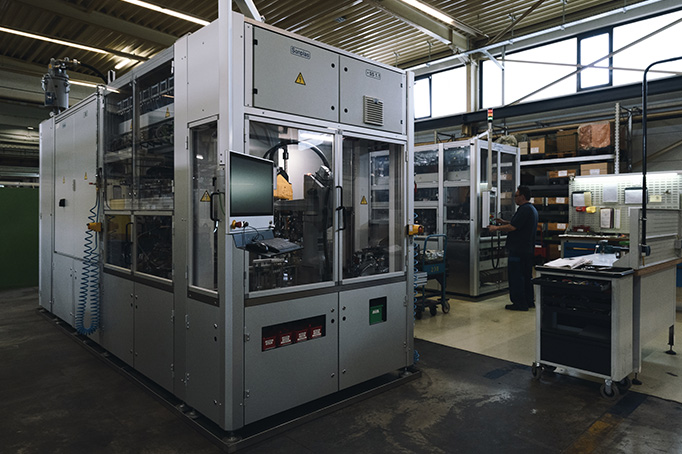
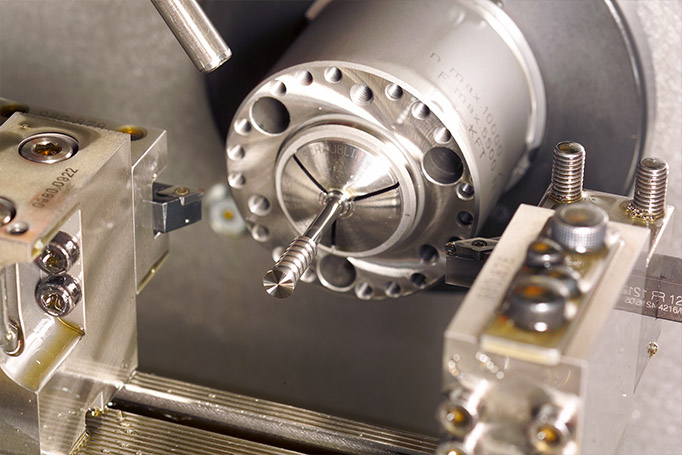
Quality at SCHUMAG begins with our people and our processes. Our integrated quality management system is the foundation of our actions, stable, capable processes are our daily routine, and highly-quality products are the result.
Preparation, monitoring and inspection are the essential components of our quality assurance in the development and maintenance of product quality.
To achieve this we have:
- integrated quality management system certified according to ISO 9001, 50001 and 14001
- 100% inspections through inline sensors, measurement evaluations and test automation, as well as random sample inspections using automated measurement sequences on coordinate measuring machines, digital measurement projectors and wave scanners
- factory testing equipment with over 7,000 hand tools, measuring instruments and measuring devices in production
- more than 40 measuring machines and devices in three air-conditioned measuring rooms
- tactile, optical and multi-sensor CMM (coordinate measuring machines)
- form measurement machines
- roundness measuring devices
- contour measuring devices
- surface measuring devices
- white light interferometers
- sampling and requalification according to IATF and VDA (PPAP, PPF)
- internal calibration of measuring equipment according to DIN EN ISO 17025
As a progressive, dynamic and future-oriented company we do not compromise on quality and environmental protection. For this reason we have defined binding standrads according to IATF 16949, ISO 9001, ISO 50001 and ISO 14001 as the working basis for each employee.
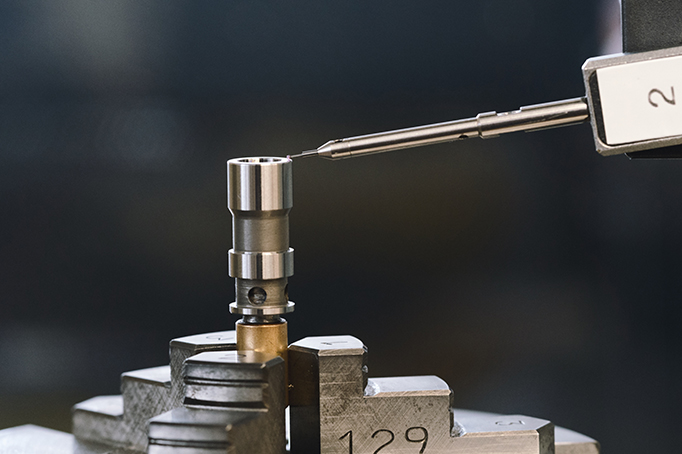
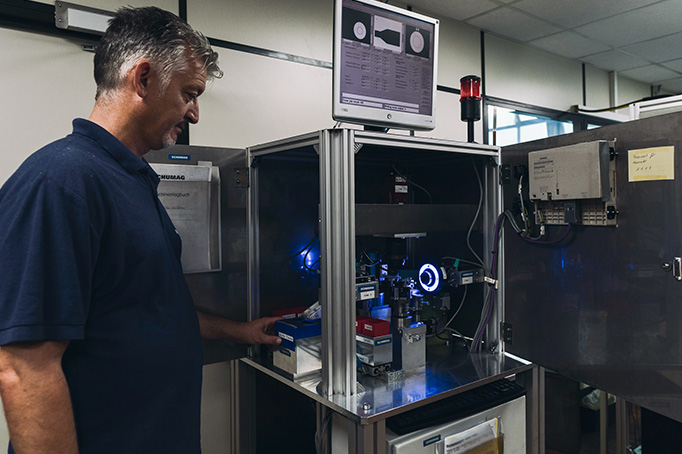
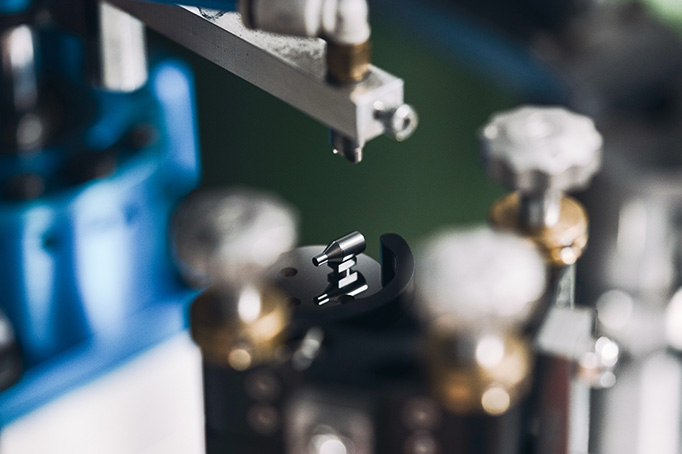
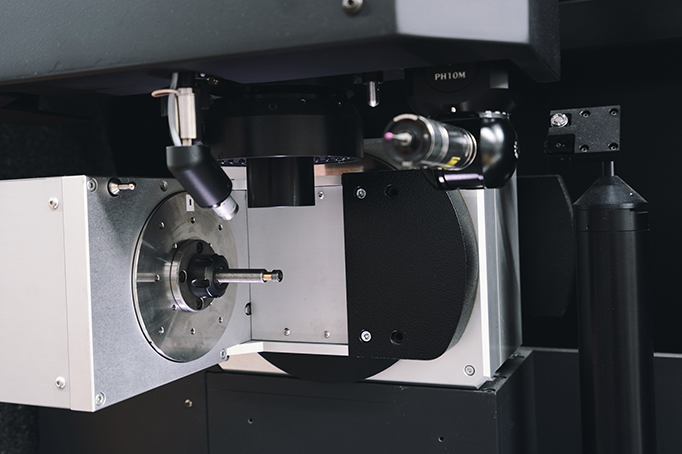
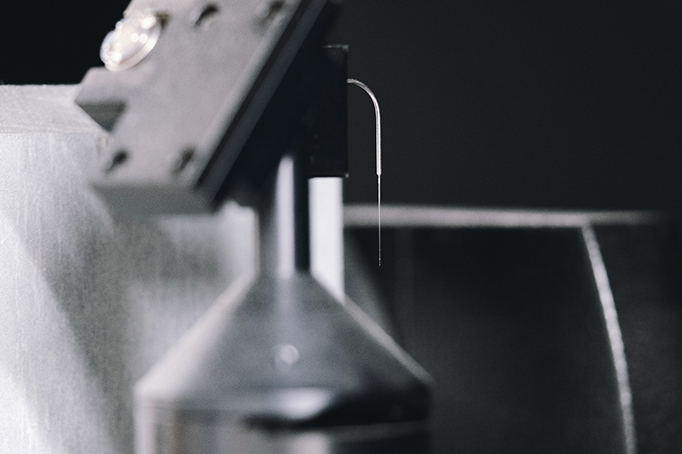
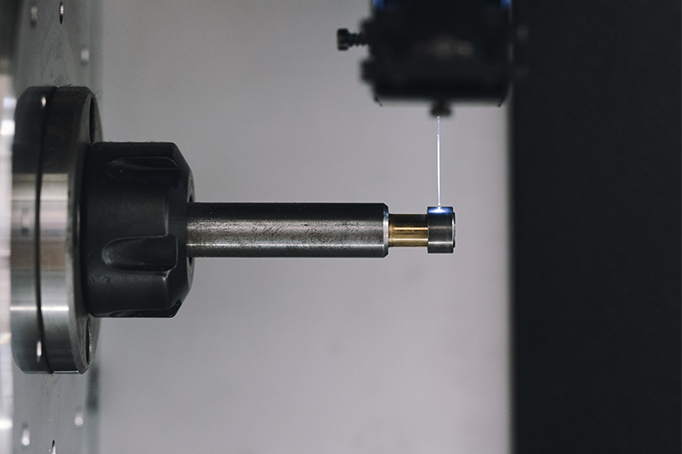
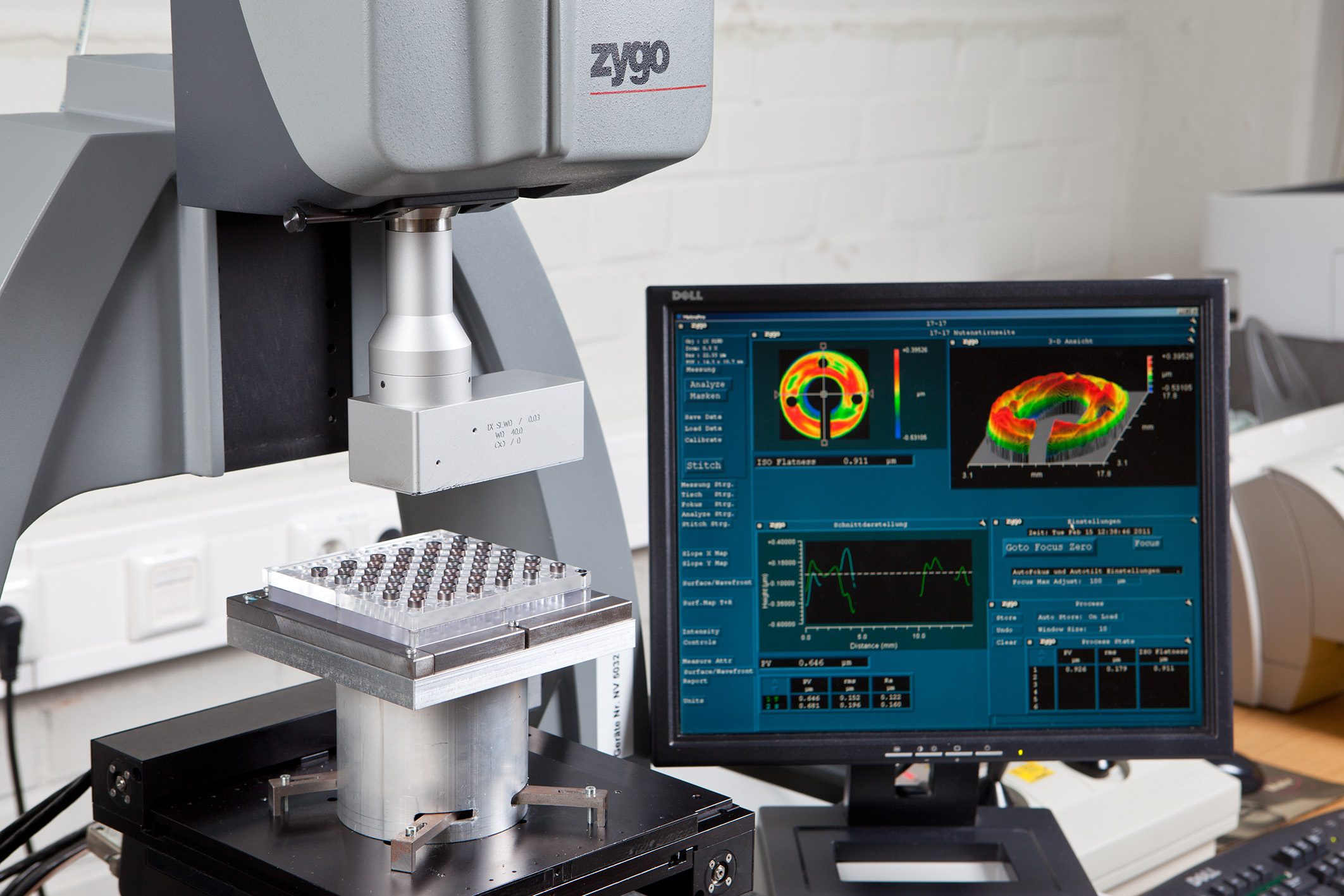
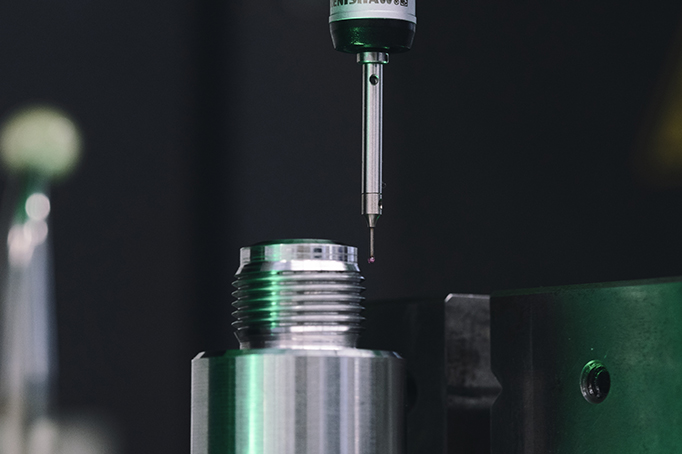
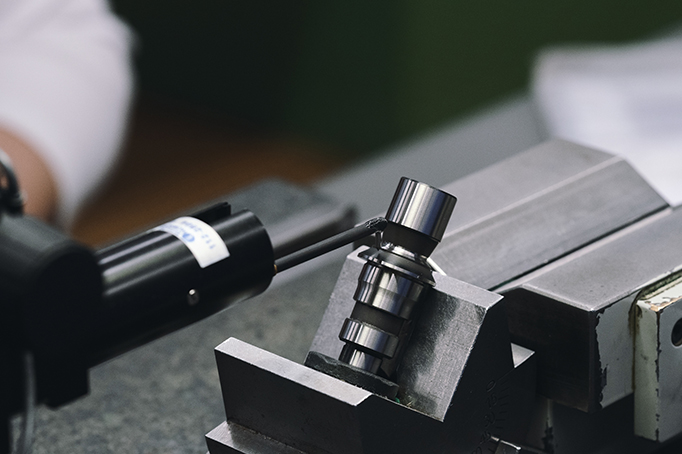
Precision lies not only in the individual part but also in the interaction of the matching components. The economic key lies in ensuring the necessary precision for reliable function with the least possible effort. In addition to manufacturing individual parts, SCHUMAG is also extensively involved in the assembly and testing of assemblies.
- special component cleaning and temperature control
- precision measurement in the sub-micrometer range and classification of components as a prerequisite for fit pairing
- assembling matching parts and assemblies (e.g. barrel & plunger combinations andas well as pressure relief valves)
- functional tests
- pressure and leakage test
- residual contamination analysis to prove compliance with the cleanliness requirements of our customers
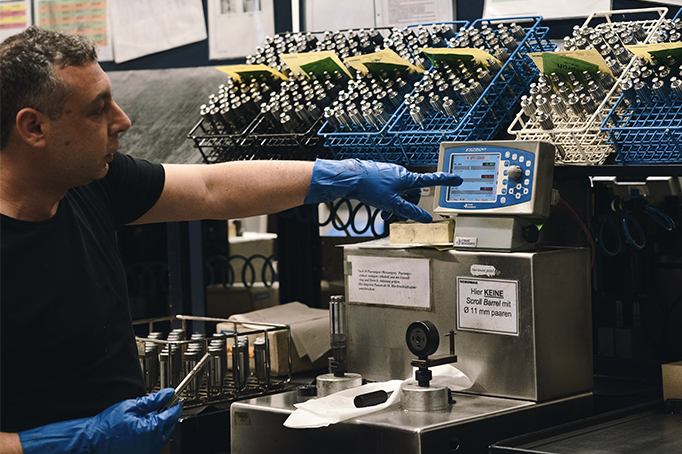
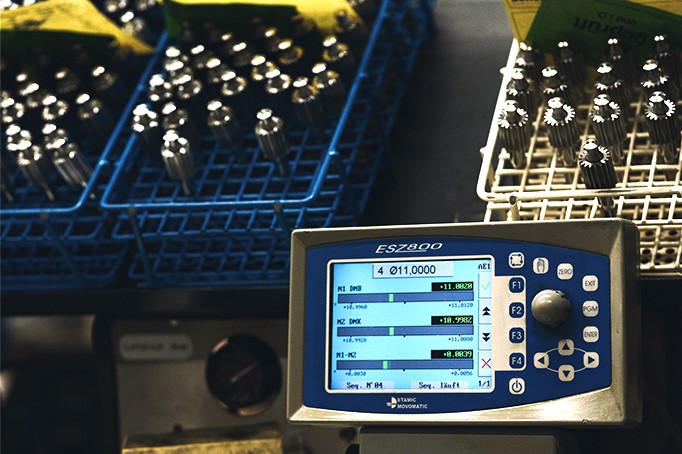
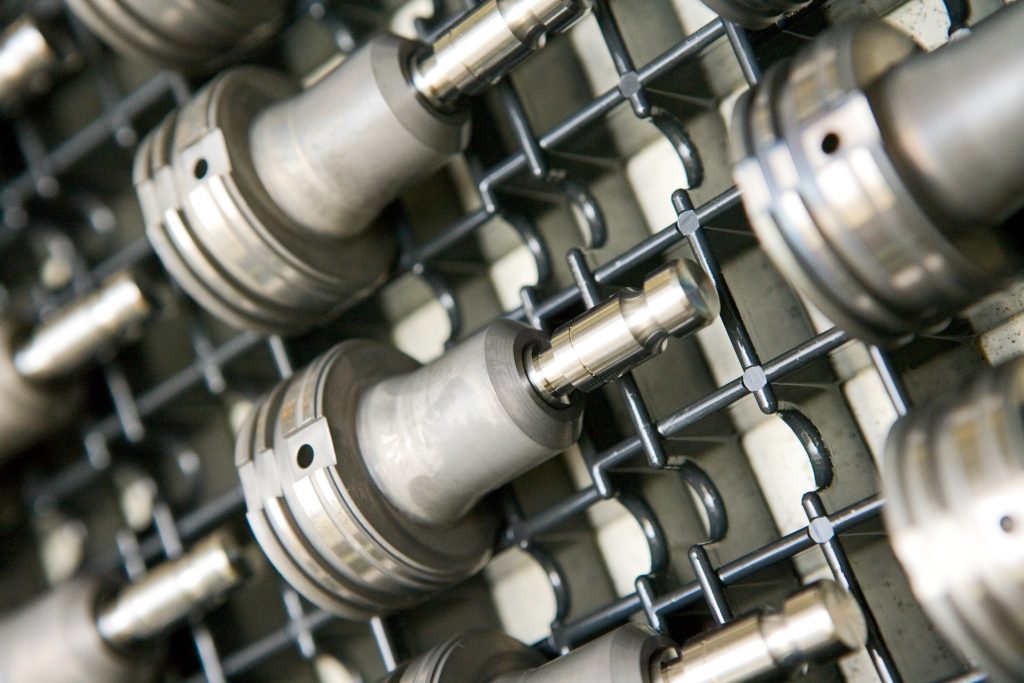
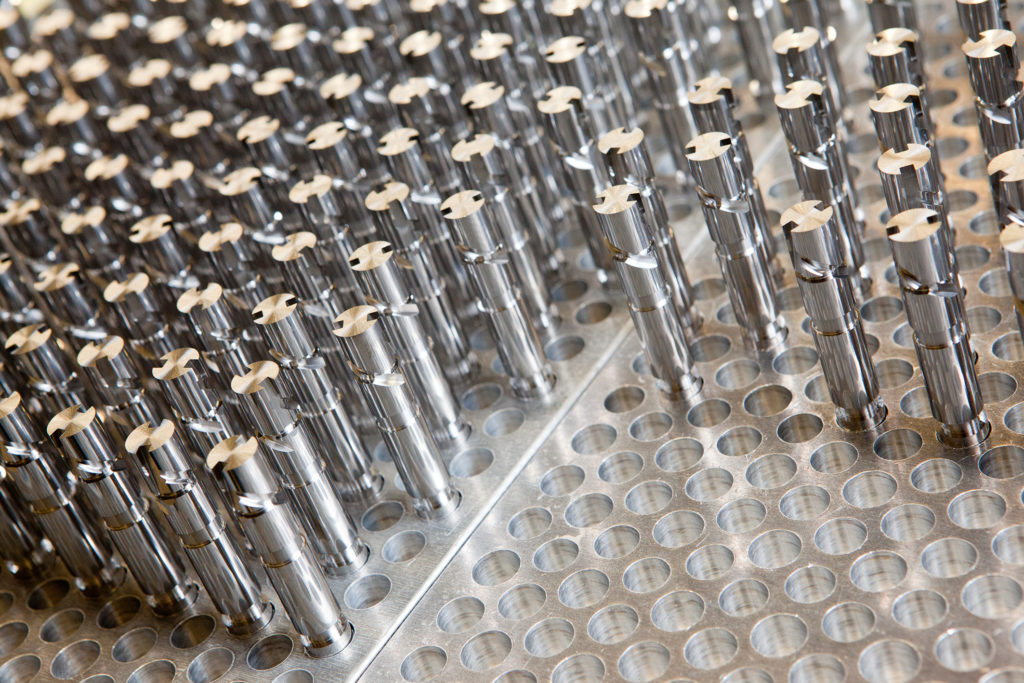
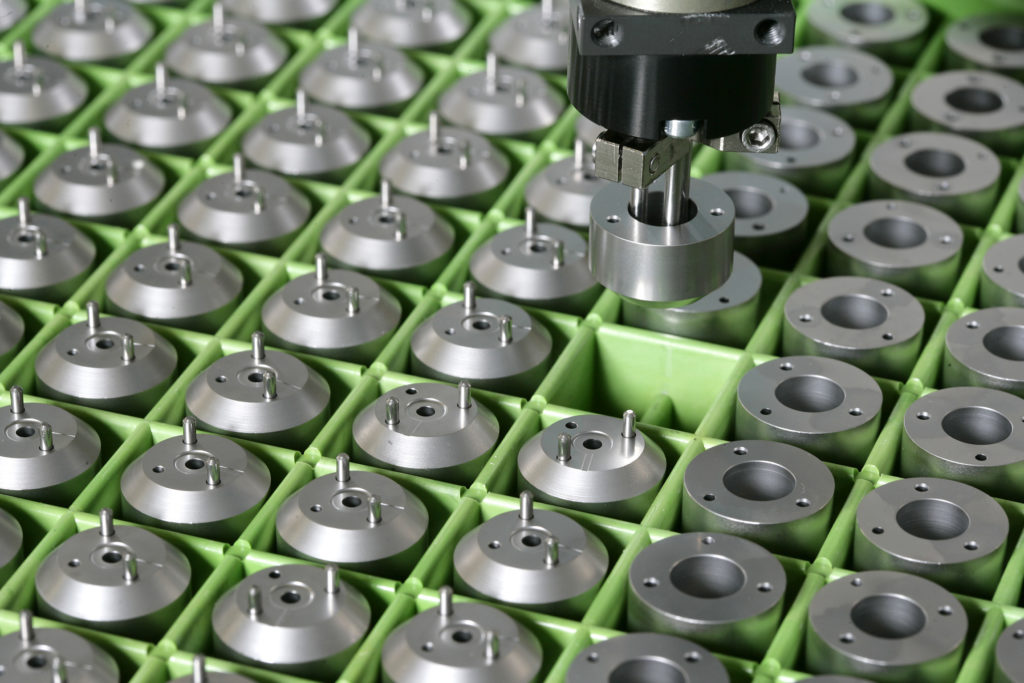
Our Markets
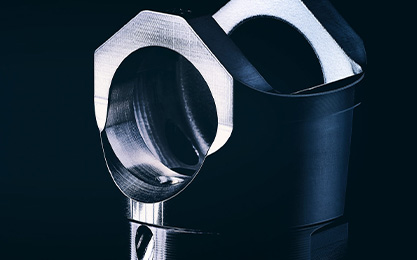
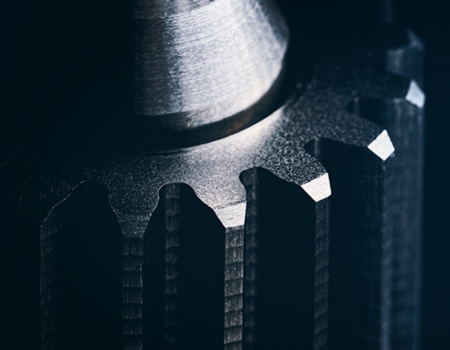
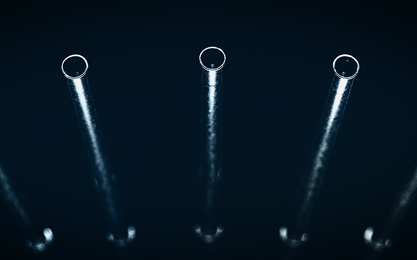
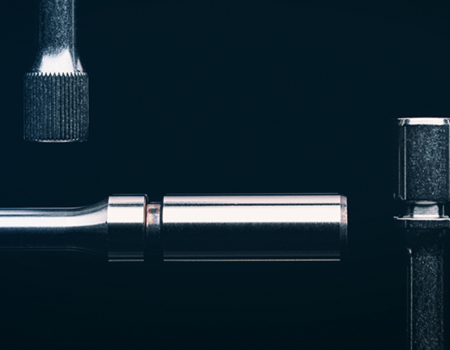
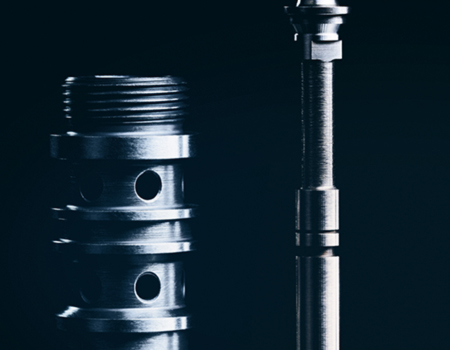
Contact Person
